Aerospace Engine
The Pearl on the Crown of Manufacturing
Aerospace engines are highly complex and precise thermal machines, the heart of an aircraft, and a culmination of manufacturing capabilities. Every significant transformation in the history of human aviation is closely linked to advancements in aerospace engine technology. The main engines equipped on contemporary civil and military aircraft are turbofan engines, and the same principles are applied in industrial gas turbines at power plants.
Turbine Blades
The First Key Component of Aerospace Engines
The power of the engine comes from multi-stage blades of varying sizes. The first key component of the engine is the turbine blade. Each blade is about the size of a palm, operates at temperatures close to 2000K, can withstand forces of up to 1.5 tons, and can reach speeds of 20,000 revolutions per minute. Such extreme operating conditions pose a significant challenge to the materials and manufacturing processes of the blades. It is essential to use ceramics as molds and employ precision casting through lost wax to arrange the atoms of superalloys in an equiaxed or single crystal state.
The processing level of ceramics directly determines the performance of the blades.
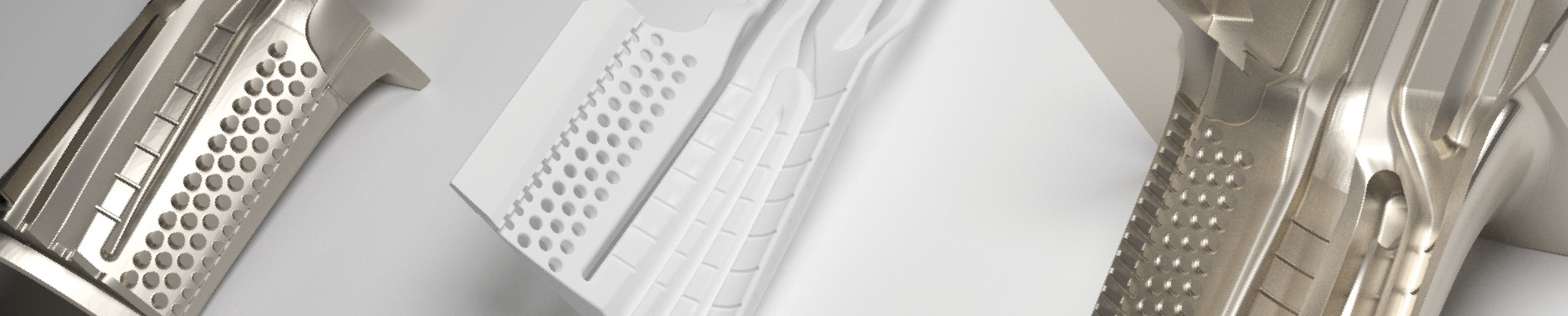
Lost Wax Precision Casting
Ceramic Core
Step 1
Digital Modeling Design
Step 2
Integrated 3D Printing
Step 3
Debinding and Sintering
3D Printing
Help customers improve R&D efficiency by 80%
Manufacture the next generation of blades
Leading abroad
We mustCatch up and surpass
Development cycle shortened by 80%
Get rid of mold processing
New product cycle shortened fromsix monthstofour weeks
Iteration speedIncreased by more than 10 times
Simultaneously try multiple design schemes
Significantly reduce trial and error costs
Rapid manufacturing
Moldless production
Manufacturing cycleShortened by 10%
Improve manufacturing efficiency
Performance qualified, quality stable
We have invested significant funds and manpower in R&D to ensure that the 3D printed ceramic cores meet the quality standards of the aerospace and lost wax casting industries. All product performances are tested according to aviation standards and meet the process requirements of mainstream domestic blade manufacturers. Each ceramic core undergoes three-dimensional dimensional inspection before leaving the factory to ensure dimensional accuracy meets customer requirements. We can currently provide various common models or in-development turbine blade ceramic cores, and also offer manufacturing services for new models.
Rapidly formed lightweight design silicon carbide mirrors.

Complex lattice structure ablation-resistant protective components.
